Осуществление обработки внутренней поверхности корпуса редуктора с использованием универсального инструмента
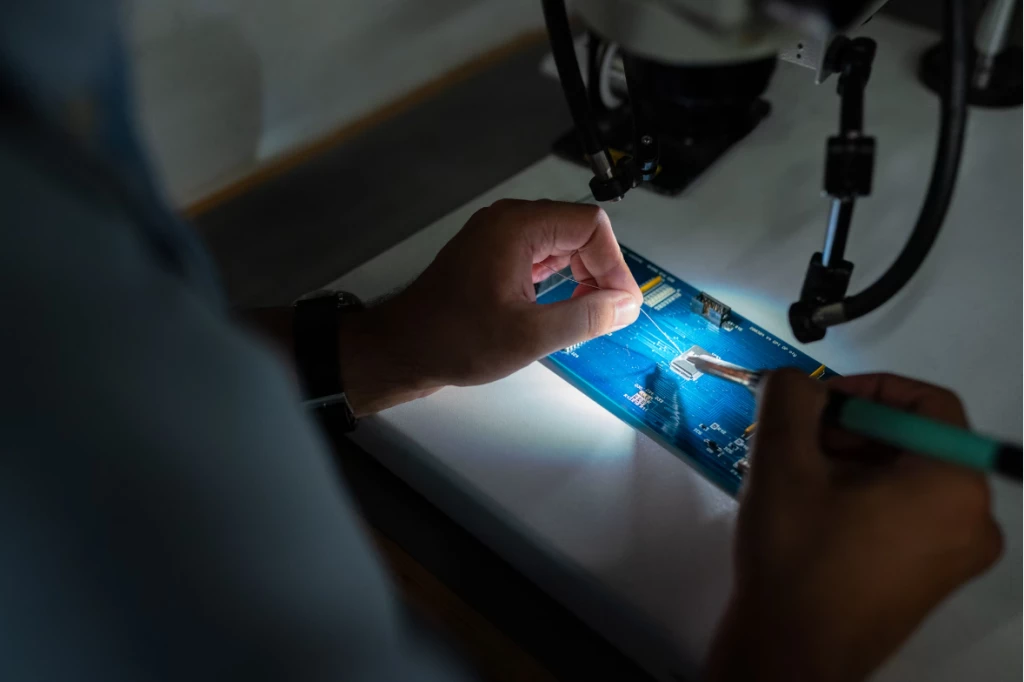
Данный материал посвящен методу обработки внутренней поверхности корпуса редуктора. Данная деталь требует внимательного отношения, разработки специального инструментария для работы с ним, а также использования наиболее современных методик обработки.
Повышение производительности механической очистки деталей в машиностроительной отрасли требует увеличения количества операций, производимых с деталями. Для сокращения данного параметра следует разработать специальные комбинированные инструменты, позволяющие оптимизировать процесс.
Благодаря использованию комбинированных инструментов, удается достичь:
Сокращения количества применяемого оборудования, что позволяет сократить расход энергии и производственные площади;
Уменьшения продолжительности технологических операций, в том числе, связанных с подвозом и возвратом инструмента. Также расход времени увеличивает наладка станков, их отдельных элементов. Сокращение всех операций приводит к росту производительности;
Увеличения точности обработки поверхности деталей.
Большинство предприятий, на которых для обработки сложных деталей применяется набор различных инструментов, заинтересованы во внедрении комбинированного инструмента. Он позволяет обрабатывать сложную деталь в один прием, избегая многоступенчатого процесса.
К деталям со сложной конфигурацией, требующей многоступенчатой очистки, относится корпус редуктора. Множество ступеней, отверстий, требует применения нескольких видов оборудования. Для замены нескольких единиц был разработан и внедрен комбинированный инструмент – зенкер.
В процессе разработки проекта требовалось решение нескольких важных задач, например – отвод стружки для сохранения работоспособности прибора. Данный вопрос был решен путем увеличения количества канавок для стружки и угла их наклона, сокращения числа зубьев, дробления стружки под действием жидкости, подаваемой под давлением.
Кроме того, проект универсального инструмента/зенкера учел небольшие отличия в диаметрах ступеней. Предполагается, что разработанный зенкер будет путем шлифовки «подгоняться» под размеры ступеней. Наружный диаметр изготавливается при этом равен диаметру набольшей ступени. В универсальном зенкере будет размещено небольшое число переточек, ограниченное размером ступени самого малого диаметра.
Обработка малого диаметра предполагается зенкером, состоящим из двух ступеней, диаметры которых равны 20 мм и 16.2 мм соответственно.
Благодаря разработке и внедрению многоступенчатого зенкера стала возможной одновременная обработка двух различных ступеней отверстия, не требующая переключения инструментов, их переналадки. Все это позволило увеличить производительность обработки и сократить ее длительность. Кроме того, уклон между диаметрами ступени инструмента дает возможность нанесения фаски. Это позволяет проводить обработку как сквозных, так и глухих отверстий, глубина которых менее 35мм, имеющих форму конуса с углом в 1200. Подобная подготовка конуса проводится перед нарезанием резьбы.
Благодаря внедрению универсального зенкера сократился расход времени на производство одной детали, что существенно увеличило показатель производительности, дало возможность избежать использования многочисленных дополнительных инструментов. В совокупности указанные преимущества позволяют сократить финансовые расходы и сделать использование зенкера более экономически выгодным.
Комментарии 0